The Unseen Cost in Heavy Machinery: 68% Component Failures Start with Subpar Pins & Bushings
Field Data from 200+ OEM Service Reports
In quarry/mining operations where pins face relentless abuse:
- Impact Loading (15-ton cyclic forces every 6 seconds)
- Abrasive Contamination (0.8mm material loss/hour in granite processing)
- Thermal Shock (-30°C Arctic sites ↔ 180°C friction zones)
What 18 Months of Failure Analysis Shows:
73% hydraulic system breakdowns originate from bushing wear patterns
64% pin fractures involve improper hardness grades for load capacity
Operators waste 22% annual budget replacing components prematurely
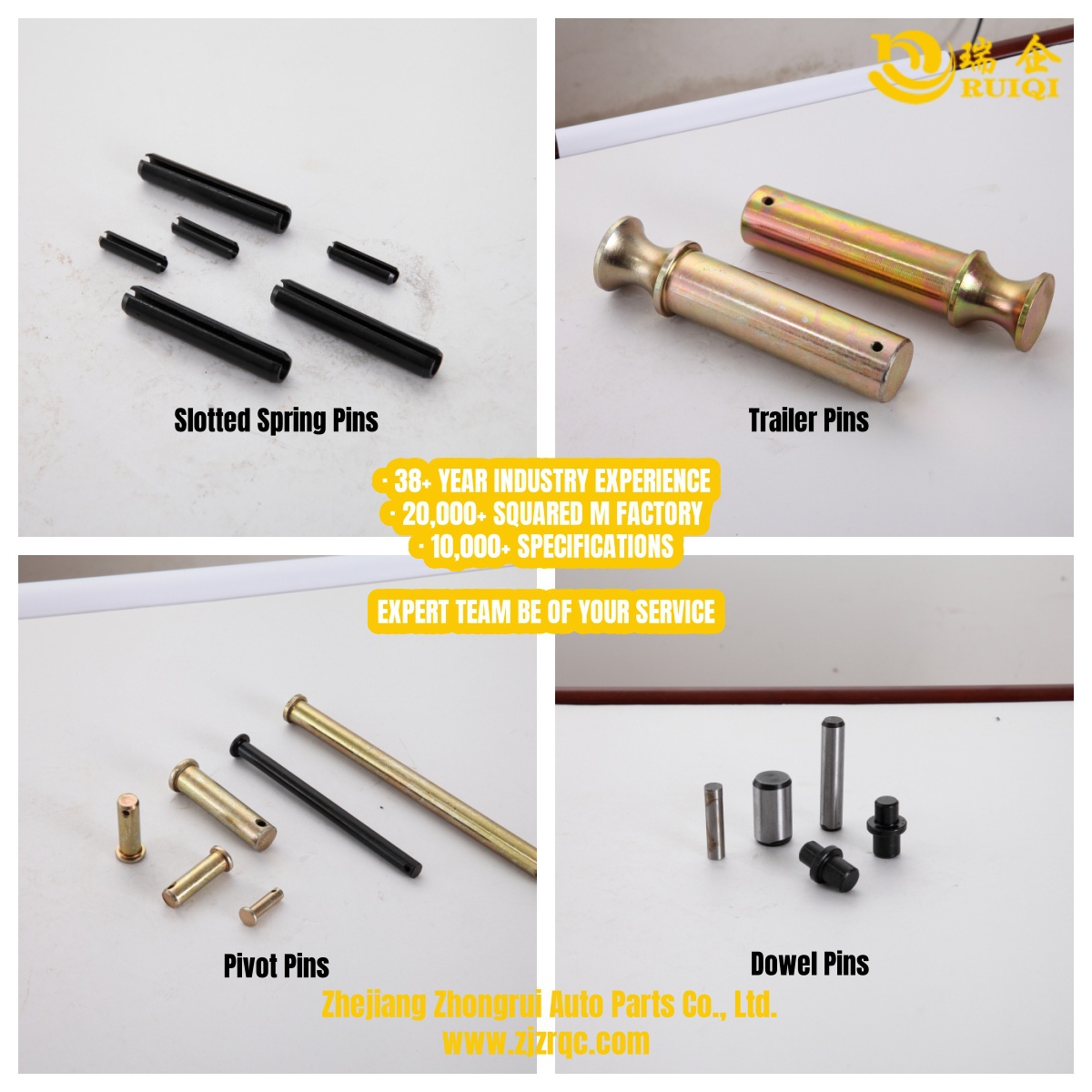
What we offer:
Precision-Engineered Pin Solutions
Verified through 800+ agricultural/construction equipment applications:
✓ Laser-Reference Wear Tracking
- 0.05mm measurement resolution (per ISO 23788 measurement protocols)
- Standard feature across all pin diameters 10-80mm
✓ Enhanced Bushing Durability
- Boron-hardened surfaces proven in:
- Combine harvesters (3,200hr+ service intervals)
- Loader pivot joints (4:1 replacement cycle improvement vs. C93200 bronze)
✓ Stress-Optimized Material Selection
- 14 certified alloy grades covering:
- 400-1600MPa yield strengths
- -40°C to 260°C operational range
Contact us
https://www.zjzrqc.com/contact/
Thanks in advance,
Zhejiang Zhongrui Auto Parts
Click Drop us a messageto get the latest catalog and quotation
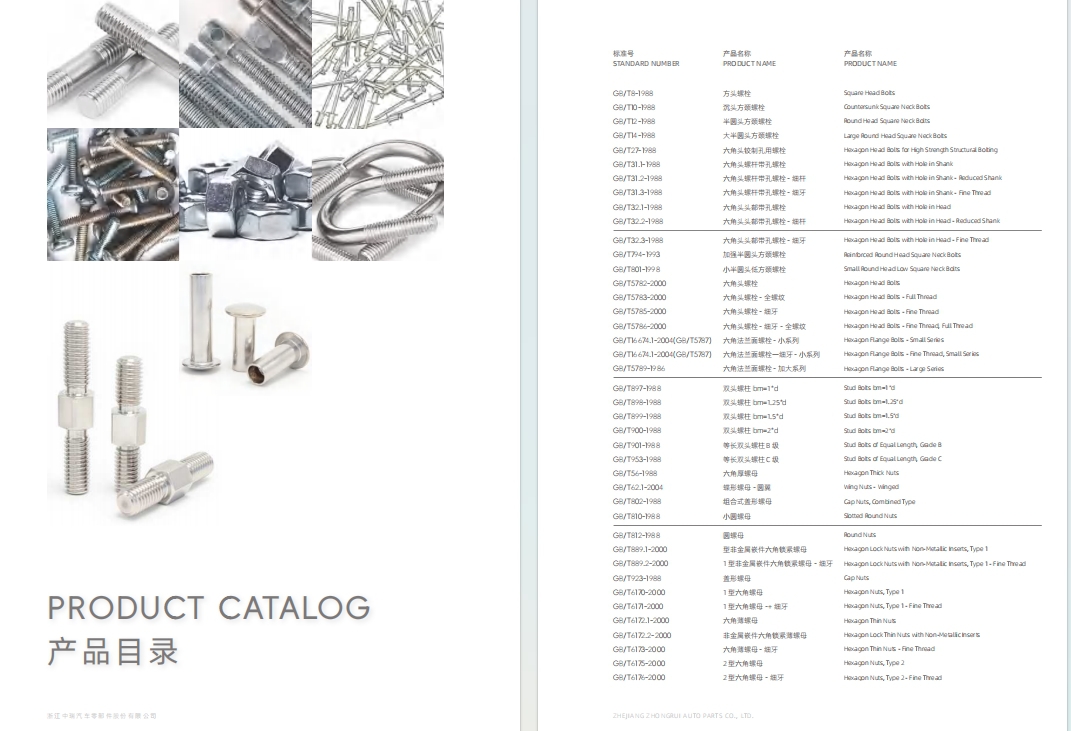